OPTX™ WA & WT
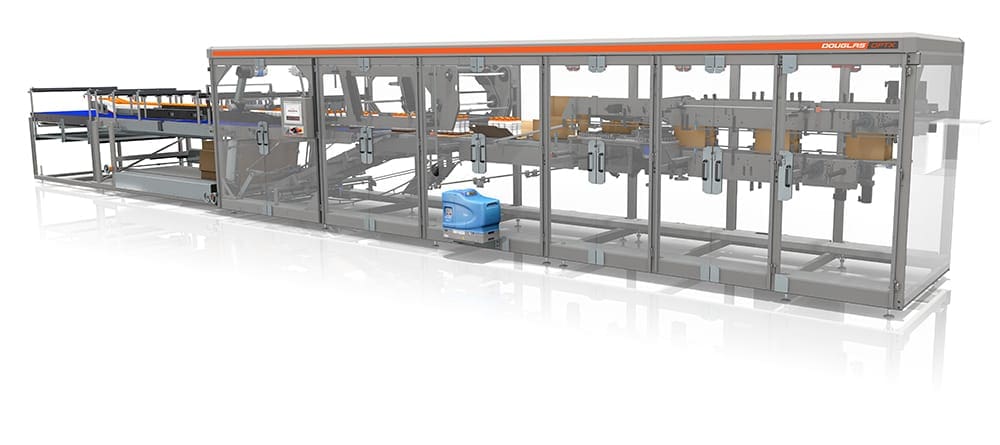
OPTX WA & WT CASE & TRAY PACKERS
High Performance for Wraparound Packaging
The OPTX WA & WT wraparound case and tray packers offer adaptable, consistent product loading as well as reliable case and tray forming and sealing. Accurately pack bottles, canisters, cartons, and bundles at speeds up to 80 packs per minute with simple SCARA metering and inline, direct loading. Control every step of the packing process with a durable, productive machine.
magazine capacity
packs per minute
changeover
(dependent on extent)
OPTX WA & WT Pack Patterns
Pack round products such as bottles and canisters as well as cartons, bundles and square-cornered containers.
OPTX WA & WT Key Features
Optional Automated Changeovers
Automatic adjustment of servo controlled changepoints reduce manual adjustments for fast, repeatable changeovers
Simple SCARA Metering
Simplified mechanisms, familiar Rockwell controls, and SCARA robot designs improve case packer function, form and duty-cycle
Improved Accessibility
Reduced Maintenance
Consistent Compression & Sealing
Precise Handling
Case blanks and products are controlled with physical lugs rather than grip belts, resulting in more accurate handling
Optimized Product Control
Flexible Product Handling
Speed
Up to 80 packs/minute
Case/Tray Types
OPTX WA: Wraparound cases;
OPTX WT: Wraparound cases and trays
Min. Case Size
6″ (152 mm) x 5” (127 mm) x 5.75” (146 mm)*
Max Case Size
20” (508 mm) x 14” (356 mm) x 16” (406 mm)*;
Max Case Blank: 27“ x 54”
Min Tray Size
5” (127 mm) x 3” (76 mm) x 9.25” (235 mm)*
Max Tray Size
13” (330 mm) x 14” (356 mm) x 22” (558 mm)*;
12” (305 mm) max vertical if shrink wrapping downstream
Magazine Capacity
10’ (3 m)
Glue System
Nordson ProBlue® Flex
Adjustments
HMI selectable recipes, automatic position actuators, threaded screws, hand wheels and hand knobs with position pointers and numeric scales
Guarding
Category 3 guarding;
Full length 1/2” (12.7 mm) acrylic guard doors (main machine) and clear polycarbonate
Electrical
Rockwell Automation (AB) programmable logic controller, servo and AC drives, PanelView+ HMI;
Washdown options available
Power
480 V; 50/60 HZ; 3 PH;
Second 480 V drop for glue unit
Air
90 PSI (6.2 bar)
*Note: Measurements indicate Direction of Travel x Vertical x Across Machine
Buy with confidence. Experience the difference.
Douglas stands behind our equipment with a 3-year limited component and limited lifetime frame warranty.