Apex™
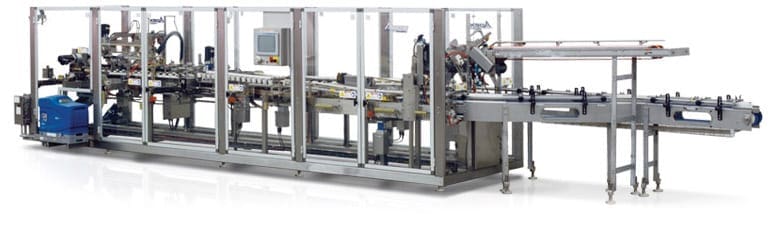
APEX SLEEVER
Compact, Mid-Speed Cartoner with Exceptional Versatility
The Vantra IM cartoner combines versatility, efficiency, and a compact footprint, making it ideal for mid-speed intermittent motion cartoning. Handling trays and cartons on a single platform, Vantra integrates seamlessly with multiple infeed types, enabling precise and gentle product handling for cans, bottles, pouches, and flow-wrapped products. Its walk-in frame design, ergonomic access, and extensive carton range capability provide flexibility and ease of operation, while its proven hygienic construction ensures long-lasting durability. Designed for cost-effective automation, Vantra IM is the perfect balance of performance and practicality for diverse secondary packaging applications.
sleeve design options
sleeves per minute
changeover capability
Apex Pack Patterns
Package single, multi-pack, and multi-tier products into sleeve designs with less paperboard material and more product visibility.
Apex Key Features
Product Handling Flexibilities
Variety of designs for infeed conveying, collating, and loading increase line efficiencies for soft, semi-rigid, and rigid containers
Sleeving Style Options
Wraparound, drop-through, or neck-through sleeving options for products including single, multipack, and multi-tiered packs
Open Accessibility
Walk-in frame provides easy access for operation and maintenance
Simplified Operation
Paperboard Sleeve Control
Choose Your Sleeve Style
Product Handling Solutions
Infeed, collating, and loading solutions offer precise product
control for a variety of product types:
Speed
Up to 300 cartons/minute;
Up to 800 products/minute (pitch, product and sleeve design dependent)
Min. Carton Size
4.5” (114.3 mm) x 1.25” (31.75 mm)
x 5.5” (139.7 mm)*
Max Carton Size
10.5” (266.7 mm) x 4.25” (107.95 mm)
x 12” (304.8 mm)*
Magazine
6′ (1828.8 mm) standard;
Shorter or longer capacities optional
Drive
Servo motors
Electrical
Allen Bradley programmable logic controller or per project specification;
Touch screen operator interface panel;
NEMA12 wiring and enclosures;
NEMA 4 or 4X wiring and enclosures (optional);
Power
230/480 V, 50/60 HZ, 3 PH
Single drop;
Other power sources available
Air
80–100 PSI (5.5-6.9 bar)
* Note: Measurements indicate Direction of Travel x Vertical x Across Machine
Buy with confidence. Experience the difference.
Douglas stands behind our equipment with a 3-year limited component and limited lifetime frame warranty.